Ausgangslage
Für die Prozessentwicklung in der selektiven Materialzerkleinerung habe ich einen flexiblen Hochspannungsimpulsgenerator in Kombination mit einem kontinuierlich arbeitenden Fördersystem entwickelt.
Der Generator musste in folgenden Parametern flexibel sein: Spannung, Energie pro Puls und Induktivität. Die Parameter sollten unabhängig einstellbar sein. Deswegen habe ich den Generator so entworfen, dass Spannungen (40kV – 200kV), Kapazität (2.5nF – 75nF) und Stufenzahl (2 – 4) über die Steuerung gewählt werden konnten.
Weiterhin sollte ein neues Konzept für die Förderung der zu zerkleinernden Materialien erstellt und umgesetzt werden: ein metallisches Förderband, das gleichzeitig als Gegenelektrode dient.
Umsetzung
Im ersten Schritt habe ich, zusammen mit dem internen Kunden, die notwendigen Funktionen, Randbedingungen und Spezifikationen in einem Lastenheft zusammengefasst. Daraus wurden mit dem Projektteam Konzepte entwickelt und in einem SWOT bewertet. Dem internen Kunden wurden die Konzepte vorgestellt und gemeinsam entschieden, welches umgesetzt werden soll.
Ich habe daraufhin einen Projektplan aufgestellt, der die mechanische Konstruktion, die elektrische Steuerung, sicherheitsrelevante Einrichtung, den Prozessablauf und das Hochspannungsdesign koordinierte. Als Projektleiter habe ich gemeinsam mit dem von mir zusammengestellten Projektteam eine detaillierte Gefahrenanalyse durchgeführt. Das Ergebnis floss in die mechanische Konstruktion ein, die durch einen externen Partner ausgeführt wurde. Alle Aspekte der Sicherheit, die konstruktiv nicht berücksichtig werden konnten, wurden in eine Sicherheitssteuerung integriert, die auch den gesamten Anlagenprozess steuerte. Die Hardwarekomponenten wurden durch die Steuerungsexperten im Projektteam ausgewählt, die ebenfalls die Software programmierten. Als Fachperson habe ich das Hochspannungsdesign übernommen.
Nach mehreren Design-Reviews wurde der Bau der Anlage freigeben. Ich habe den gesamten Bestellprozess geplant und überwacht. Für den Aufbau der Anlage habe ich die Ressourcen in der Produktion gesteuert. Bei Unklarheiten während der Produktion war ich Ansprechpartner und für kritische Spezialkomponenten habe ich die Qualitätskontrolle übernommen.
Während des Aufbaus der Anlage habe ich ein umfangreiches Testprogramm entworfen und die Tests zum grössten Teil selbst durchgeführt. Verschiedene Situationen aus der Gefahrenanalyse wurden simuliert, um die Sicherheit der Anlage zu testen. Am Schluss konnte ich die Anlage dem internen Kunden übergeben. Sie wird erfolgreich in der Prozessentwicklung für externe Kunden eingesetzt.
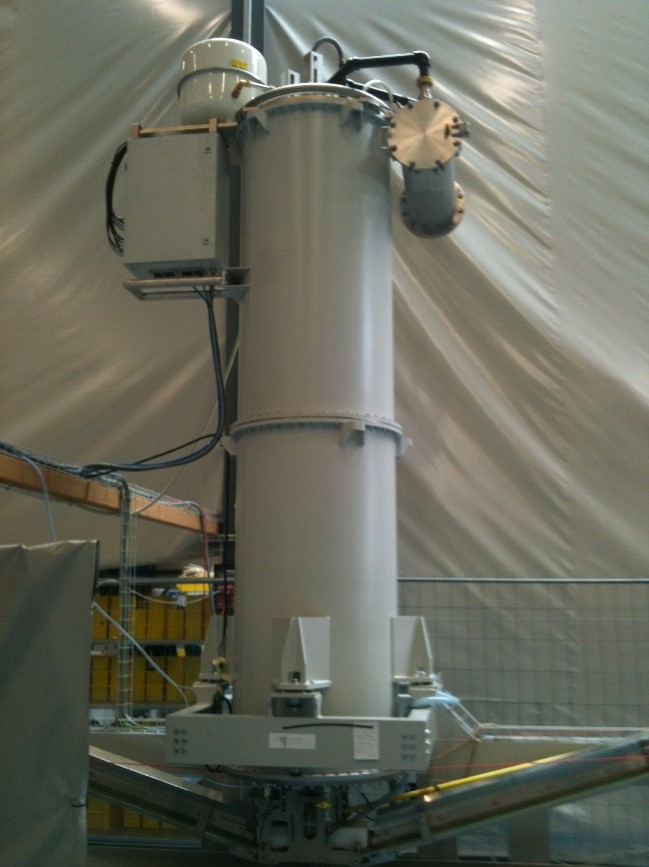

Ziele und Kennzahlen
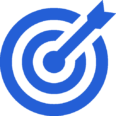
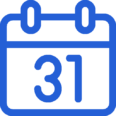
März – November 2011
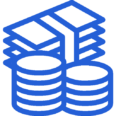
Budget 400’000 CHF
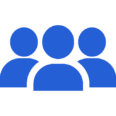
Sechs Mitarbeitende im Team

Maschinenbau- und Elektroindustrie
