Initial situation
For process development in selective material comminution, I developed a flexible high-voltage pulse generator in combination with a continuously operating conveyor system.
The generator had to be flexible in the following parameters: voltage, energy per pulse and inductance. The parameters should be independently adjustable. Therefore I designed the generator so that voltages (40kV – 200kV), capacitance (2.5nF – 75nF) and number of stages (2 – 4) could be selected via the controller.
Furthermore, a new concept for conveying the materials to be fragmented was to be created and implemented: a metallic conveyor belt that also serves as a counter electrode.
Implementation
In the first step, together with the internal customer, I summarized the necessary functions, boundary conditions and specifications in a requirements specification. From this, concepts were developed with the project team and evaluated in a SWOT. The concepts were presented to the internal customer and a joint decision was made as to which one should be implemented.
I then created a project plan that coordinated mechanical design, electrical control, safety-related equipment, process flow, and high-voltage design. As project manager, I conducted a detailed hazard analysis together with the project team members I have put together. The result was incorporated into the mechanical design, which was carried out by an external partner. All aspects of safety that could not be taken into account in the design were integrated into a safety control system that also controlled the entire plant process. The hardware components were selected by the control experts in the project team, who also programmed the software. As a specialist, I took over the high-voltage design.
After several design reviews, construction of the facility was released. I planned and supervised the entire ordering process. For the construction of the plant, I managed the resources in production. I was the contact person in case of uncertainties during production and for critical special components I took over the quality control.
During the construction of the plant, I designed an extensive test program and carried out most of the tests myself. Various situations from the hazard analysis were simulated to test the safety of the plant. In the end, I was able to hand over the plant to the internal customer. It is successfully used in process development for external customers.
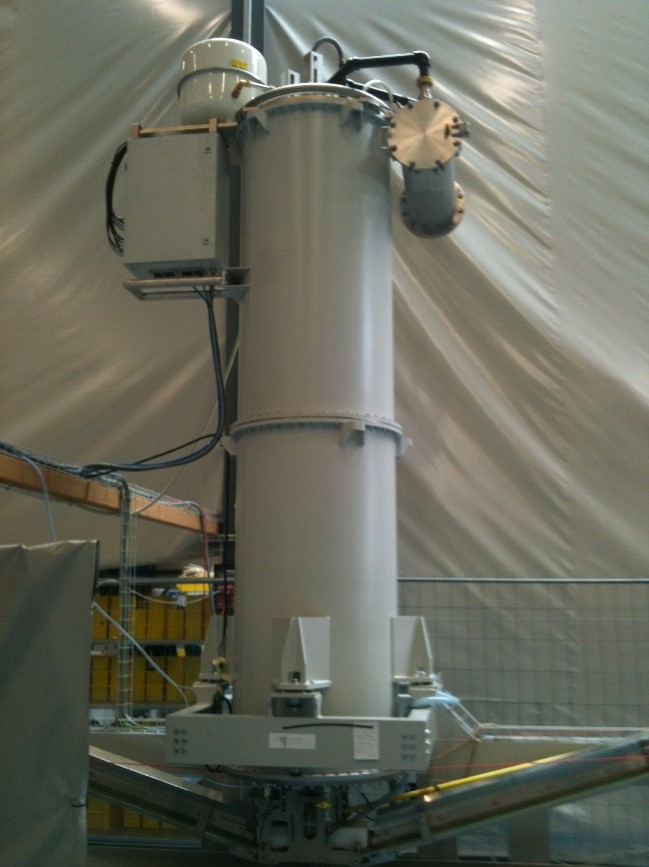

Targets and key figures
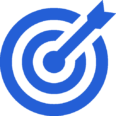
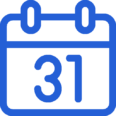
March – November 2011
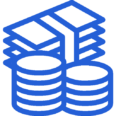
Budget 400’000 CHF
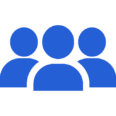
Six employees in the team

Mechanical and electrical industry
